What is the IP Class & IP67?
The Ingress Protection (IP) Class is an international standard that aims to provide end-users with detailed product information regarding ingress protection. Rather than relying on loose marketing terms such as waterproof, the IP Class indicates the exact degree of protection against the intrusion of solids or liquids.
The IP67 refers to a product’s protection from total dust ingress, as well as protection from water immersion between 15cm and 1 metre.
How is IP67 awarded?
In order to be awarded Ingress Protection Class IP67, an item must be immersed in 1 metre of water for 30 minutes without any water entering the enclosure. This confirms whether or not the item is at risk of water damaging the electricals inside.
How does IP67 relate to Helium Leak Detection?
A recent experiment, conducted by INFICON, helped to determine the correlation between water and gas leak rates.
The experiment involved creating a test part with interchangeable artificial leaks of various sizes made of glass capillaries ranging from 10-40 µm. The test part was filled with water, pressurised to 1.1 bar absolute pressure (the same pressure in 1m of water), and observed for 30 minutes. Materials other than glass were also tested, including PVC, aluminium, and steel.
The two graphs below show the correlation between water leakage through a leak in 30 minutes, and the corresponding gas leak rate through the same material and leak size.
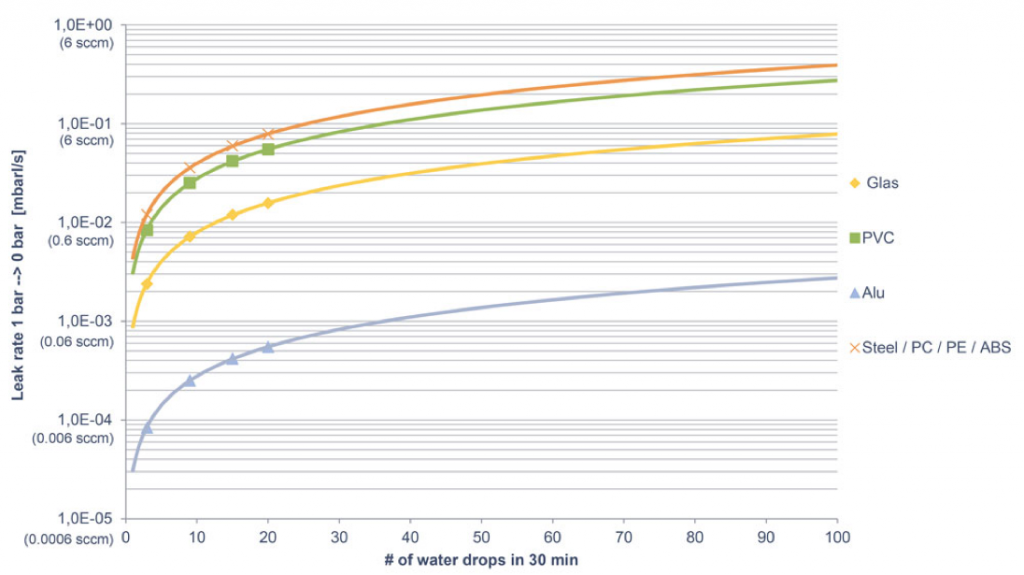
Graph 1: Leak Rate for 100 mbar Differential Pressure
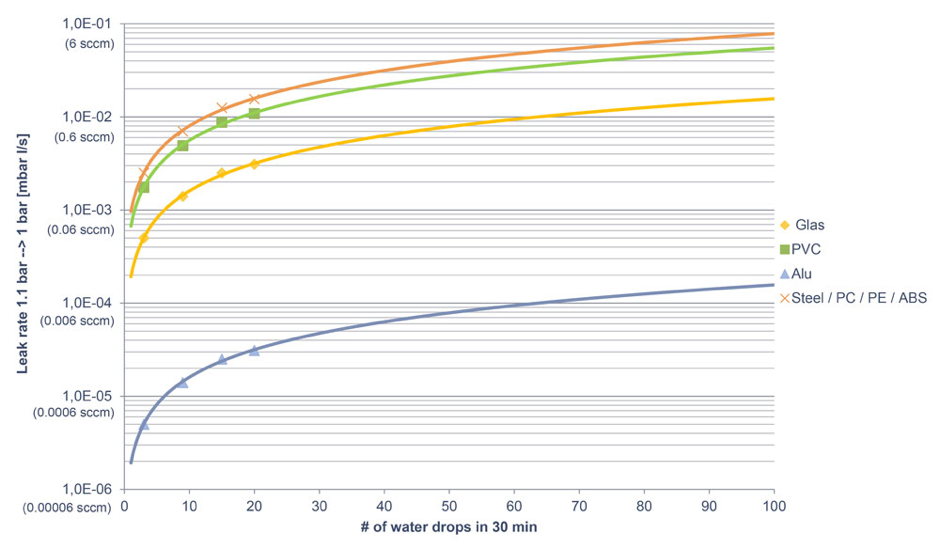
Graph 2: Leak Rate for 1 mbar Differential Pressure
Applying the graphs
In terms of pressure settings, it is important to differentiate between overpressure leak testing (1.1 bar to 1 bar) and vacuum leak testing (1 bar to 0 bar), as some parts can be damaged by even relatively low changes in pressure.
Depending on how much water your part can tolerate, you can work out the maximum gas leak rate to test for using these results. This can be done by testing the part using water and using the graph to find the estimated gas leak rate. You can then use this information to hone your leak testing into those measurements, saving time and resources, such as tracer gas.
For example, Graph 1 shows the leak rate for 100 mbar differential pressure. Testing a steel component with this method, you would receive the best results in the low 1*10-2 mbar l/s (0.6 sccm) range if you can withstand a small leak, or 5*10-3 mbar·l/s (0.3 sccm) for a more complete seal.
The graph also allows you to estimate leak rates for mixed materials. For example, on Graph 2, detailing the leak rates for testing at 1 mbar differential pressure, if your material is made from aluminium with a polymer seal, making the leak path half aluminium and half polymer, the estimated leak rate would be roughly halfway between the two materials on the graph -at around 1*10-4 mbar·l/s for a low leak rate, or the mid 10-5 mbar· l/s range for a more secure seal.
Conclusion
According to INFICON leak testing for ingress protection according to IP67 requires sensitive leak testing methods that can test well below 1 sccm leak rates. Tracer gas leak testing is the method of choice for these applications.
Different materials and pressures will require different leak rate specifications.
If you’d like to learn more about this subject, please contact us today.